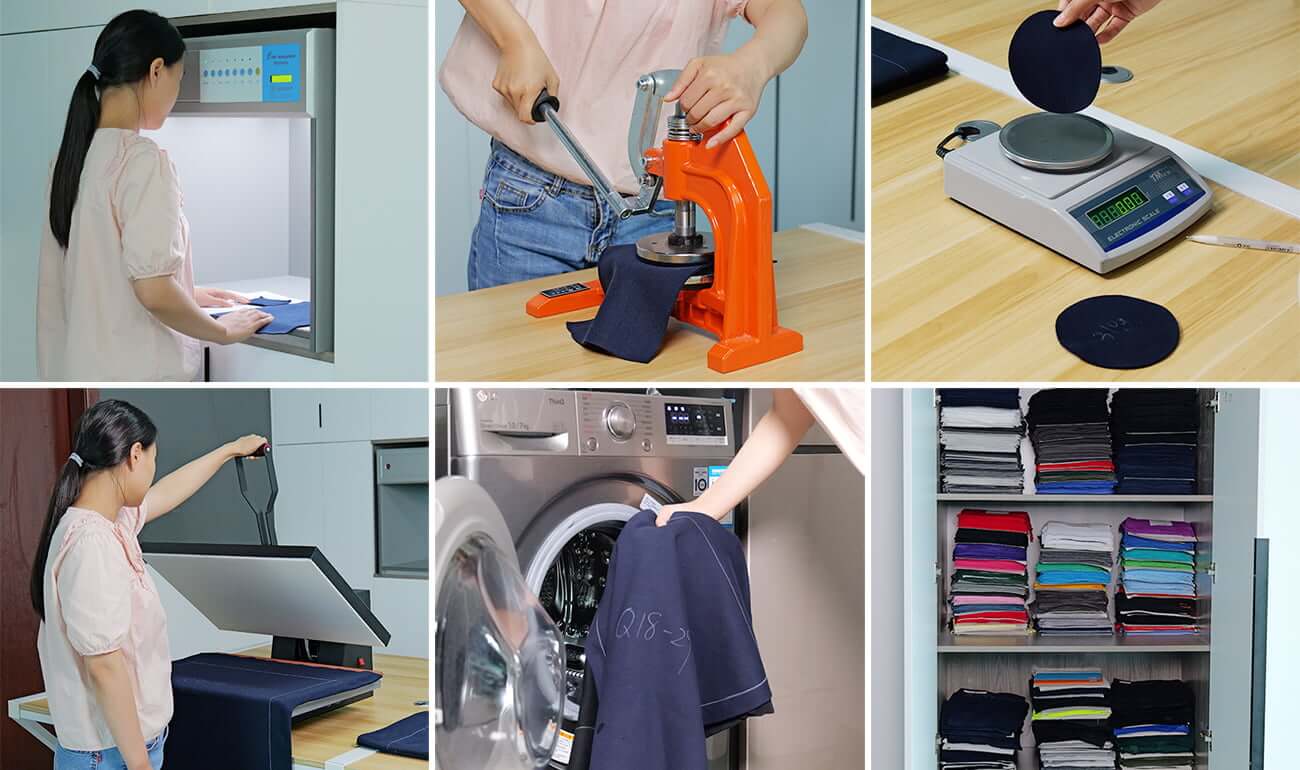
STEP 1
Fabric Quality
Control
We consistently control the color shade and quality of the fabric. For every dyeing tank, we carefully assess the color, the texture and the weight. We check the heat shrinkage, wash shrinkage, color fastness, etc. We even store the approved fabric swatches to keep the color the same shade all the time.
STEP 2
Cutting Piece Quality Control
We unroll the approved fabric to make them unstretched and loose for 24 hours. And we sort the cutting panels by dyeing tank. But for some kind of sensitive fabric or color, we cut lot by lot instead of tank by tank to avoid color shade on one piece of garment. Each cutting panel must be inspected to make sure there is no defect on the fabric.
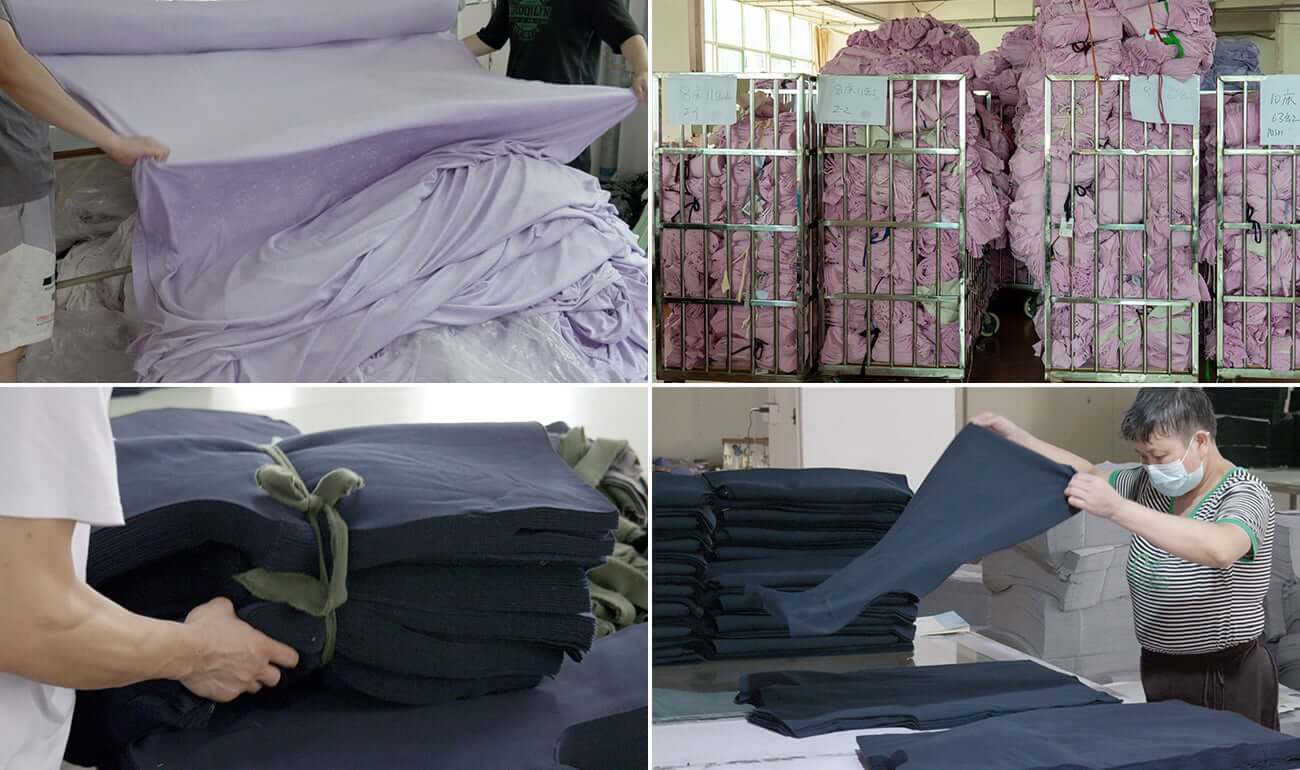
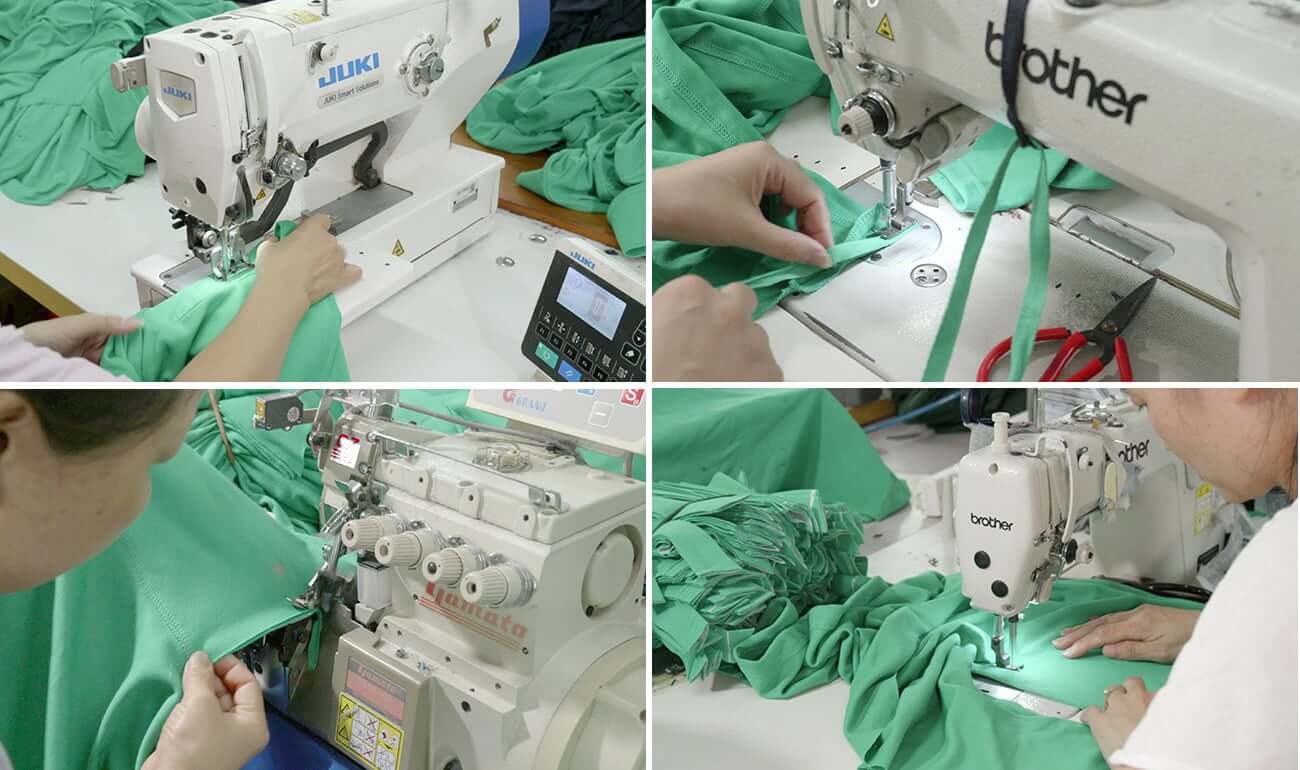
STEP 3
Experienced
Workers
Over 20 year experienced workers plus famous brand computer production equipment like Brother, Yamato and Juki realize computer ERP networked order production management. Thus the quality is improved and output is increased.
STEP 4
Garment Quality
Control
The vacuum board for sucking floating thread can clear all the thread-thrums on the garments. Then each piece of garment must be inspected before packing. After all the apparels are packed into cartons, our chief QC will draw some cartons randomly to do the final inspection based on AQL 2.5 or AQL 4.0 standard to make sure the quality is assured. We load the cartons size by size, color by color and style by style in order, which is very convenient for our customers to unload the goods.
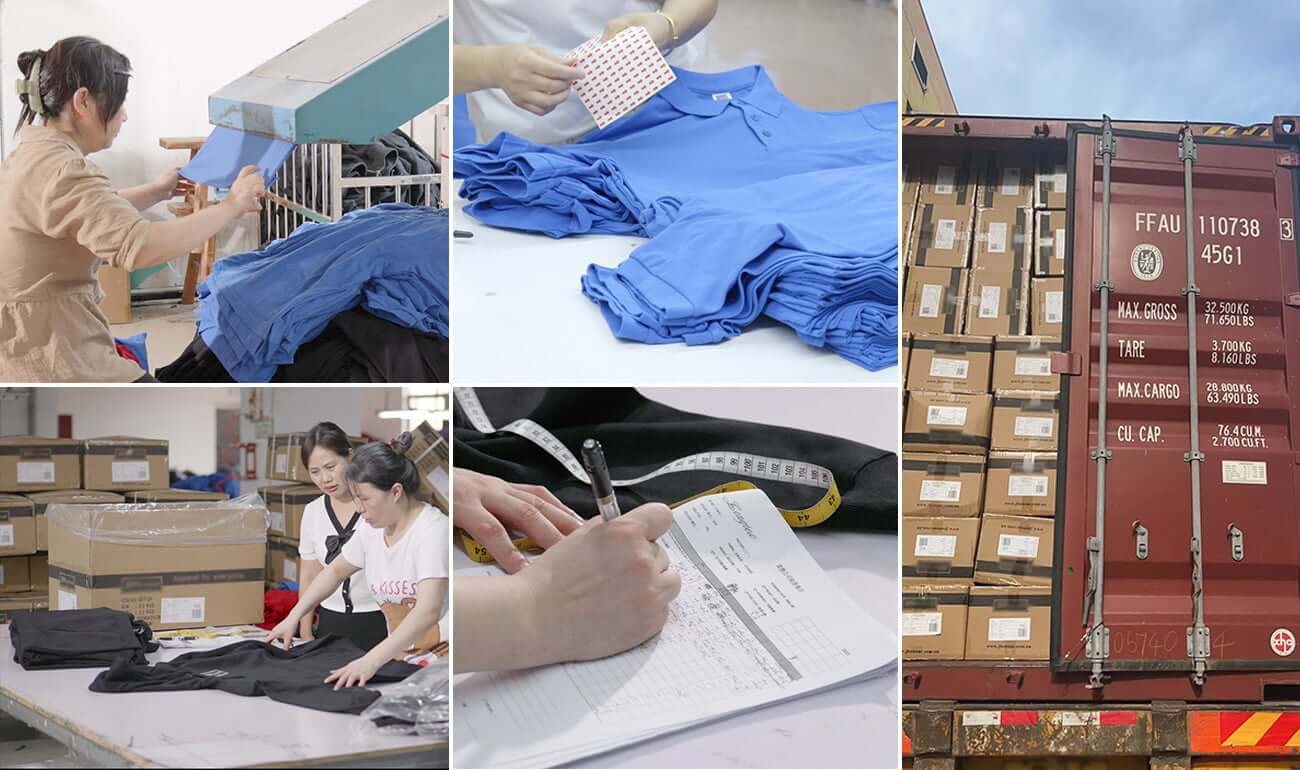